Voltage/Current Waveform Analysis
Charts showing some of PQView’s analysis functions available from power systems monitors that record voltage and/or current samples.
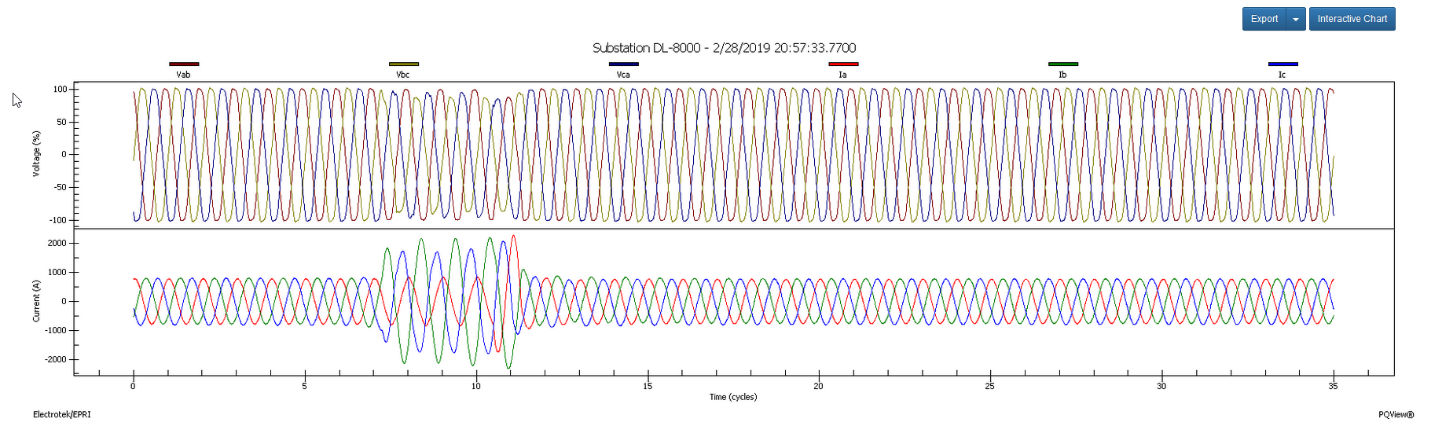
PQView offers Voltage and Current Analysis via Derived Charts.
All charts can be download it to JPEG, PDF and other known formats for your convenience.
PQView 4 charts allow you to apply filters to your data, such as high pass filter, low pass filter and it provides their properties. It also gives you the ability to customize the derived charts.